Are you looking for the different rivet types and uses? You are going to find answers to all the questions you have about the different types of rivets we have and how they can be used in this article.
However, before we consider the rivet types and uses, let us have a better understanding of what rivets are.
What are rivets?
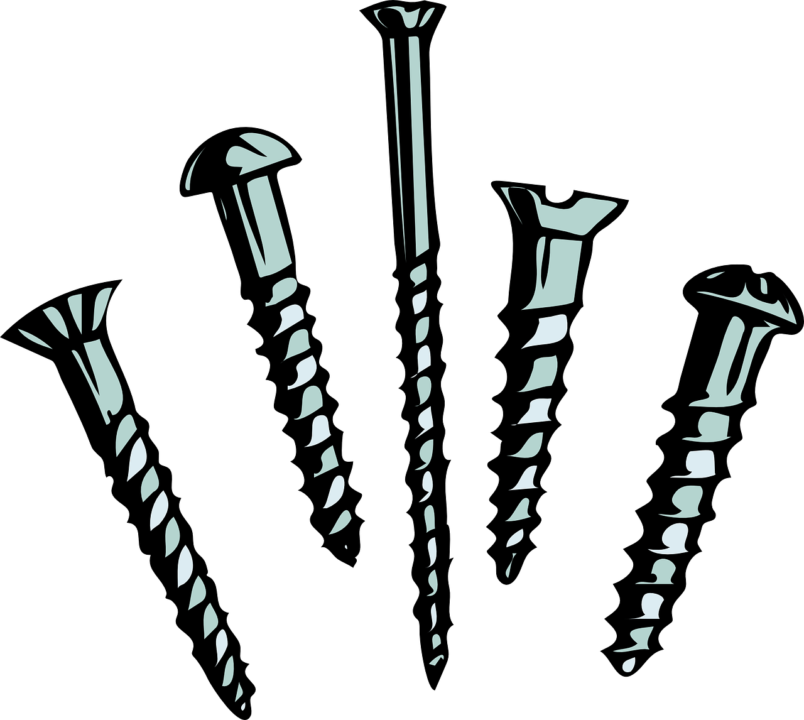
Another alternative name for rivets is blind fasteners. Rivets are fasteners that are used to join two sheets of metal or plates together by forcefully inserting them into holes so that they form rigid and permanent rivet joints.
A rivet has a head and a cylinder, which are made from either aluminum, steel, or other materials. The instruments used for installing rivets are known as riveters and they can be secured into sheets either by drilling or punching.
They are used for fabrication work in industries such as the engineering industry for joining bridges, in the automobile industry for joining cars made of aluminum, etc.
Now let’s consider rivet types and uses one after the other.
Rivet Types and Uses
1. Solid Rivets
Solid rivets come first on the list of the rivet types and uses that we have because they are the most common types of rivets. They are the oldest known method used for joining materials.
These tools have a strong shaft and a head on one end, which gets formed immediately when they are punched in. While the headless part at the other part of the rivet is deformed when it is punched in.
Major typesets consist of shafts and heads; they usually get deformed with a rivet gun or hammer.
Most times, solid rivets are used in situations where safety and dependability are paramount. For instance, they can be employed in the structural components of an aircraft.
2. Tubular Rivets
Tubular rivets have some similarities with solid rivets and they have a hollow shank. They are mostly used for drilling items such as shoes, file covers, etc.
They are versatile, making them applicable for use with materials such as aluminum, thin metal sheets, leather, and other pivot areas where mobility is needed.
Another name they are popularly known as is ‘hollow rivets’ This name is given to these types of rivets because of their hollow body ends.
The types of tubular rivets we have include the following:
-
Compression Tubular Rivets
These are types of tubular rivets made up of two parts that fit tightly during the fastening process. These rivers are commonly used for materials that are soft and require aesthetic consideration on both sides of the components.
-
Semi Tubular Rivets
Semi-tubular rivets are a special kind of rivet with holes at the end of their shank. The depth of the hole is usually about 1.12 of the diameter of the shank, giving the semi-tubular rivet a solid-like feel when the field head is formed.
-
Full Tubular Rivets
One of the features that distinguishes full tubular rivets from other types of rivers is that they have deeper holes. They are not as strong as semi-tubular rivets but they can pierce softer materials, such as fabric and plastic, easily.
3. Pan head rivets
Pan-head rivets are another rivet type that are known for their unique and outstanding designs. Their heads are round and they usually slope down right from the top.
These designs of rivets are produced from carbon steel, brass, copper, aluminum, and stainless steel. They generally come in varying lengths, ranging from 6mm to 100mm.
They are often used for structural works that are heavy-duty and need high-gripping or support.
4. Countersunk Rivets
One other major rivet type is the countersunk rivet. These types of rivers are best for use in situations where it is necessary to have a flush surface on the plate so that they project the rivet head freely.
The reason they are called countersunk rivets is because they are used as countersunk holes. They are also widely used in aircraft to improve aerodynamic smoothness.
They are mostly available in three different types and they are classified based on the neck angle of these rivets. The three major rivets, which are:
120° Shank, 90° Shank and 60° Shank respectively.
5. Mushroom Head Rivets
Mushroom head rivets are the types of rivets that are usually used to take the height of the rivet head on the surface of the metal to help give them the needed locking and support.
The heads of these types of rivets are like those of much room and the materials used in the production of these types of rivets include alloys, titanium, and nickel alloys.
6. Flat Head Rivets
These types of rivets have a rounded, flat, and solid cylindrical shape, which makes them the best option for sealing joints rotating joints, and performing other types of industrial work that involves fastening solid material together.
They enter easily into the objects intended for joining without requiring so much force, like the solid rivets. Another name they are called is slotted rivets.
7. Flush Rivets
Flush rivets are among the rivet types we also have. Flush rivets are the types of rivets that are designed to remain sited on the surface of the metal and cannot exceed the surface level.
They are commonly used on airplanes, where the major concern is aerodynamic drag.
8. Self pierce Rivets
Self-pierce rivets are the type of rivets that do not necessarily need a hole before they are used. They can be used to join two solid objects together, even if they do not have a hole or space where the rivets can enter.
They have a special feature that allows them to pierce through objects on their own, which is why they are referred to as self-pierce rivets. The material used in manufacturing self-pierce rivets is stainless steel.
This is how they work when they are used, they create an airtight seal between two metal sheets by piercing through the upper layer fully while the lower part is only partially penetrated.
The installation process of self-piercing rivets includes positioning, holding, piecing, stamping, foaming, and setting.
9. Blind Rivets
Another name blind rivets are called or are known for is hollow pop rivets. These are metal fasteners with cylindrical shapes with a mandrel positioned in their center.
Blind rivets are fastened into pre-drilled holes that are separated and intended to be joined together by manufacturers.
The mandrel breaks off when the blind end expands, and the installation of blind rivets can be done by the side of the parts, making it difficult for the rear part to be visible.
Blind rivets are the best option when it comes to trying to view the back end of a joint. They are the most commonly used types of rivets in industries like the aerospace industry.
The application of blind rivets does not come with much difficulty; applying them is fast and easy.
There are different types of blind rivets, some of which include the following:
-
Pull-mandrel rivets
Pull-mandrel rivets are a unique type of double countersunk rivet that is created to create a flush surface finish on both sides of their applications.
One of their unique features is that the head of the mandrel remains intact, which ensures that the clamping force stays consistent and remains intact.
-
Threaded rivets
Another type of blind rivet is the threaded rivet. These types of rivets are known as threaded inserts. They offer a wide range of solutions to manufacturers.
These rivets can be anchored to one part of the installed part, simplifying the assembly process. They are of two forms: the standard and the heavy-duty threaded rivets.
-
Drive-pin rivets
Drive-pin rivets are a special type of blind rivet that have short mandrels protruding from their heads. Their mandrels can be expanded with a hammer when they are inserted into a hole.
These types of rivets are commonly used for architectural works, as their application makes them unnecessary for pre-drilled holes. However, when compared to other types of rivets, they offer a lower clamping force.
Uses of Rivets
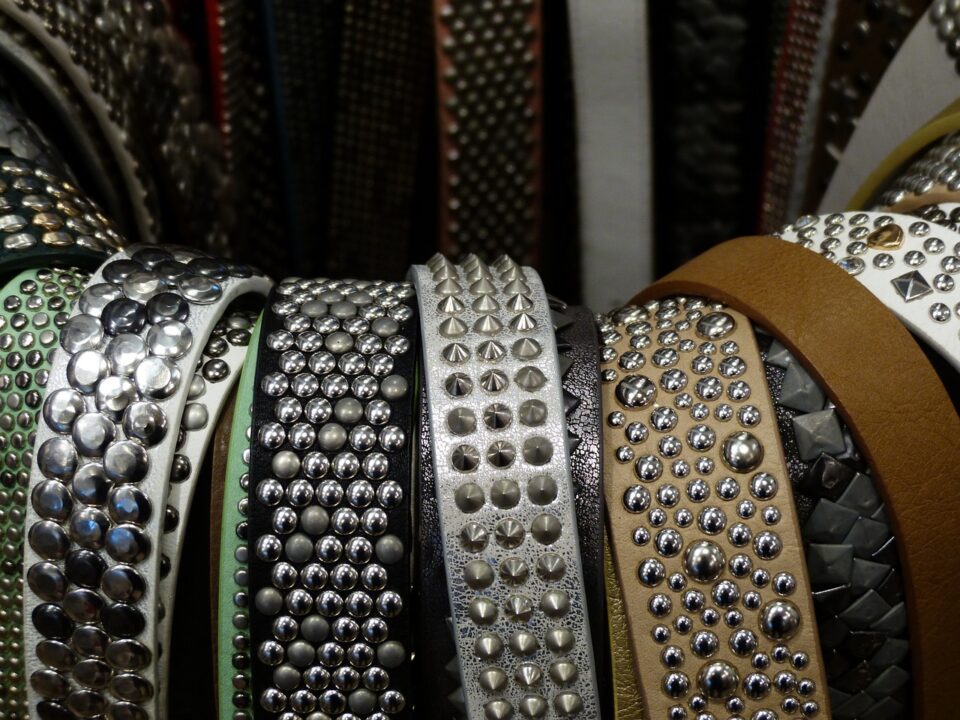
1. Rivets are used for structural works
Rivets are used for structural and construction purposes. For example, they are used in construction works such as when a bridge has to be built.
You will usually find some of the rivet types that have been mentioned above in this article on big bridges.
Rivets are used for home improvement and building. Rivets are used for installing things both inside and outside the house.
They can be used to install objects such as hanger straps, woodwork, and hinges in the house.
2. Flush rivets are used to minimize aerodynamic drags
Flush rivets are used for aircraft construction processes. For example, flush rivets are used to reduce aerodynamic drag by setting the flush rivets on the surface of the aircraft, which contributes to improving aerodynamic efficiency.
3. Rivets are used for building jewelry
Rivets are used for making jewelry. They are used to combine different elements of a jewelry design to form a piece of jewelry.
4. They are used for ship construction
Since rivets are known for joining two metal pieces together, they play a major role in ship construction because the parts of a ship are mostly made of metal, so rivets are used to join these metal sheets together.
5. Rivets are used for decorating ceilings and walls
Rivets can be used for the decoration and design of the ceiling and walls of the house. They can be used for decorating objects like wall shelves and decorative mirrors. Hanged pendants, wall wood keys, e.t.c